Technical Solutions
Desuperheating involves several challenges, from the mechanical design to temperature control systems. Cavitation can result from too high pressure drops being taken over a single pressure stage or component. Flashing can be caused by too low water pressures or too high water temperatures. Both can result from inappropriately designed or selected water valves or spray nozzles, or a change in operating conditions. Temperature control systems depend on operating conditions, response time of control systems, rangeability and operation of control valves, and placement of temperature sensors. A temperature sensor placed too close to the water injection point can be subject to spray water droplets, throwing the measurement off. Coupled with a temperature control system controlling the spray water flow, this can result in system instability.
Installation
Pipe bends and branching pipe connections can cause rotational forces in the steam flow. They can also result in spray water hitting the pipe wall if installed too close to a desuperheater. Spray water can also hit pipe walls or welds resulting in cracks due to thermal cycling. Inappropriately designed draining systems can result in free water accumulating in the steam pipes which can cause damage to valves and pipe systems.
Magnetite and other particles in steam
Magnetite coming loose from pipe walls can be carried downstream with the pipe steam and cause clogging in trims and desuperheater internals. Valve plugs can become stuck, stopping the valve from being able to close or open. Particles can erode seat sealing surfaces, causing leakage, or control elements changing their functionality.
Noise
Acoustics in steam conditioning valves are of great importance. High pressure drop and flow rates generate high levels of noise emission which can pose challenges in maintaining acoustic requirements. Steam conditioning valves reduce stream from a higher-pressure level to a lower pressure level by use of pressure reducing stages. Noise levels depend on the pressure distribution over these stages, their drill patterns and noise abatement provided by insulation. Each valve designed by BVT is uniquely optimized based on operating conditions present.
Erosion damages
Wet steam and particles result in erosion on trim parts. If erosion affects sealing surfaces, this might result in valve leakage and overheating of downstream piping. This is most common after supercritical pressure drops, where particles and steam have very high velocity. It is also more common when the valve is operating at a small opening degree.
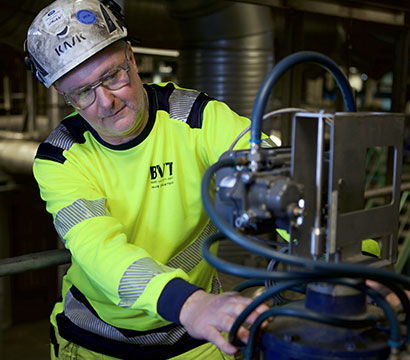
BVT remote assist
New pressure bench
Critical valve seats ready for delivery!
Commissioning
BVT has developed a series of tools for use in commissioning our valves, and protecting their internal parts during steam blowing, acid cleaning and hydrostatic pressure testing of the steam / water piping.